In business, change is inevitable. Navigating a fluctuating industry while staying ahead of trends and techniques is not an easy job. Sometimes this change can prove to be a struggle, as a company cannot adapt to the environment it finds itself in. However, sometimes change –and the recalibrating that comes from it—can lead to exciting new beginnings. Multi-disciplinary piping company Stainless Piping Systems is the leading high purity systems provider in Canada and its decades long journey is testament to the positive power that change can bring. SPS was formed in Toronto almost 35 years ago. The acquisition, and potential relocation of their employer to Wisconsin was the impetus for a team of highly talented employees to go out on their own. The group of seven, consisting of welders, engineers, and fabricators turned the turbulence of a take-over into Stainless Piping Systems. Now, thirty-four years of dedication and hard work later, SPS has firmly established itself as a reliable and successful company, all thanks to the leap of faith taken by the original team.
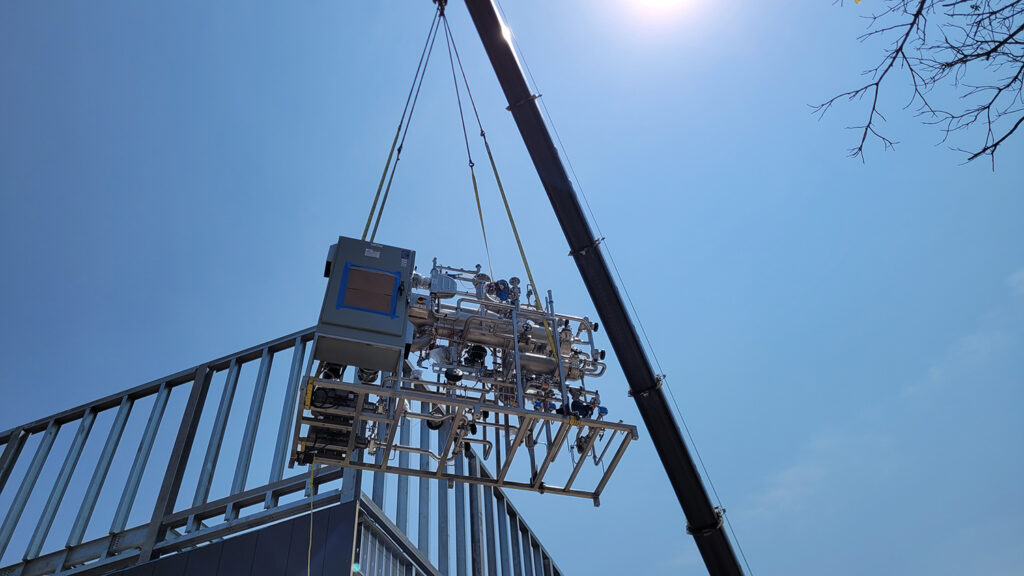
The company’s success is built on providing excellence across three main pillars: design, fabrication, and installation. The reason for this is a simple one. In a sector such as piping, accuracy and excellence is essential. By ensuring the details are adhered to, things move well from there. At SPS it is no different and for the company, the design element is a key component. Every other aspect of a quality project flows from it. In fact, design is the backbone of what it does. The company’s engineering team work collaboratively to produce accurate and detailed mechanical designs that incorporate fabrication and installation considerations. For Dave Damen, President and Senior Project Manager of Stainless Piping Systems, design is the aspect of the business that has adapted and developed most since the company’s inception in the late eighties. State of the art computer software has allowed SPS the ability to fully harness the power of design. With a strong design in place, fabrication can be executed in confidence. “The art of modern fabrication means that there is virtually no need for rework and no need for trim allowances either.” So, when it comes to installing the piping, Damen feels that the company is in a very good place. He believes that this comes down to the time, energy, and skill that SPS puts in up to that point. “With open communication and a well-integrated team, we can install successfully. This is because we have been working with the same game plan, the same information, and the same accuracy of fabrication.”
“Our work in design, fabrication, and installation, always contains pinpoint accuracy and that allows us to meet the needs of any project.”
For Stainless Piping Systems, meeting the highest standards across these three pillars are non-negotiable. In meeting the design, fabrication and installation needs of a client, the company is ensuring that its processes are maintained. Not only are they an essential part of the company’s promise to deliver an excellent service, but they also help to ensure that as a full-service pipe system provider, the company does not run into unnecessary delays or hitches. SPS can guarantee and trust the accuracy of its design, fabrication and installation and provide full-service pipe systems on every job, every time. As Damen explains, what benefits the current client also benefits future clients. “By ensuring that our systems run smoothly, we can maintain a seamless, headache-free transition from process to process. No rework is needed, and things just get done right the first time.”
Working across a number of sectors such as pharmaceutical, medical, automotive, and the food and beverage industry can bring challenges. Due to the variables and uniqueness of each industry, it is imperative that the company maintains strict and efficient internal processes. For SPS, adherence to the three pillars of its process give it the ability to adapt and serve all customers, regardless of the project. “Our business model remains consistent. Our work in design, fabrication, and installation, always contains pinpoint accuracy and that allows us to meet the needs of any project.” As Damen goes on to explain, the company has invested much time and effort into developing effective communication strategies between its departments. “We use cloud-based software to communicate designs, from concept right down to final install.” This involves the collaborating and sharing of fabrication drawings which eliminates the need for large hard copy drawings. “With the cloud-based software, every member of every team has access to the most up to date specifications and drawings, while also having previous revisions on file.”
With that in mind, it is no surprise to learn that the company has been involved in many high-profile projects, delivering some hugely impressive results along the way. One such project was a 150,000 sq ft vaccine production facility in Toronto, Ontario. The facility’s budget was half a billion dollars and involved an astonishing 27 kilometers of high purity piping. All piping on the project, which began in 2017 and finished in 2020 just as the COVID pandemic was beginning, was prefabricated, and held in storage until needed. At its peak, the piping was installed at the phenomenal rate of 650 ft per day. Damen believes that this speed and accuracy truly sets the company apart from its competitors. “It was virtually unheard of in the industry and the project stands as the benchmark of Canadian pharmaceutical construction projects. When executed properly at blistering rates, you can still maintain quality, timeliness, and efficiency.” Additionally for Damen, the company’s involvement in these structures felt hugely important and, while the success of the project was hugely positive in itself, the significance of the work being done was not lost on anyone. “This was at a moment when the call for vaccines became critical to protect the health of Canadian citizens. We eagerly did as much as we could to aid the implementation of vaccination infrastructure.”
Due to the timing of the project’s completion, and its track record of working successfully in the pharmaceutical sector, Stainless Piping System has subsequently worked in a number of new geolocations on similar projects. The company installed high purity systems in Nova Scotia and Saskatchewan among other provinces. Currently, it is working with a leading pharmaceutical company in Toronto. The major expansion project will ultimately provide flu vaccines, not just for Canadians, but the entire world.
While word of mouth and maintaining a stellar reputation are clearly an effective method of generating business for the company, Stainless Piping Systems ensures that its future is one that is built on its past successes. This is a company that develops lasting relationships with its clients and credits much of its ongoing success to repeat business. As Damen explains, it is vital that the clients it works with develop and enjoy a sense of trust. Without this, he says, customers simply wouldn’t return. “Quality, cost, and time are all equally important to our clients. By ensuring we stick to our rigorous processes, we can deliver the best possible quality in the most efficient manner, thus meeting timelines and budgets. By consistently delivering on this, we build trust. Our customers know that we can handle their project efficiently without fear of failure.”